Event report
March 28, 2023
FabCafe Global Editorial Team
At the Fuji Textile Week, the Tech Working Group of FabCafe and Loftwork presented a prototype installation that skillfully merged traditional Japanese textile making and architecture expertise with the latest technology to transform fabric into a spatial and tactile experience.
Original article in Japanese: Yutaro Gokan and Naoya Tsuchida.
English translation and editing: Judit Moreno.
Fujiyoshida City in Yamanashi Prefecture has been a hub for textile manufacturing for over 1,000 years. In recent years, the city has gained attention for its bold collaborations with artists and creators. Among them is the annual Fuji Textile Week, which aims to revitalize and promote textile innovation by blending local resources and various forms of expression.
FabCafe Fuji, the fifth FabCafe in Japan, was one of the main venues for Fuji Textile Week 2022, and hosted many of the program’s events and exhibitions. One of the standout exhibits was presented by the Tech Working Group, a unit within FabCafe and Loftwork, under the Fringe Program category.
The installation focused on exploring “space utilization” as a new application area for smart textiles. By collaborating with traditional weaving manufacturers in Fujiyoshida and individual creators such as architects and engineers, the Tech Working Group presented a prototype that provided a five-sense “spatial experience” to users.
The ECHOES 00_CUBIC installation is a cube of fabric that reacts to changes in the environment. The flow of lights and sounds from the cube in turn alters the mood of the room it is placed in, creating an ongoing dialogue with the surrounding space.
The textile cube is made up of conductive fabric, which reacts to the static capacitance present in the environment. When people approach or touch the cube, the capacitance they carry affects the fabric, causing the light to sway.
The key to the success of the ECHOES 00_CUBIC prototype lies in the effective combination of traditional manufacturing procedures, advanced digital technologies, and free creativity. The project relied heavily on technical knowledge for efficient monitoring and progress.
The project manager, Technical Director Naoya Tsuchida, reflects on this point.
-
Naoya Tsuchida
Technical Group, Technical Director
After graduating from university, Tsuchida worked as a system engineer on the development of next-generation car systems, including smartphone integration and a car software platform, gaining expertise in embedded software. In 2021, he joined Loftwork, where he combines technology with a creative perspective to design products that contribute to user well-being. He also works on individual projects focused on the relationship between people and technology by incorporating the concept of Calm Technology. His hobbies include collecting gadgets and drinking tea.
After graduating from university, Tsuchida worked as a system engineer on the development of next-generation car systems, including smartphone integration and a car software platform, gaining expertise in embedded software. In 2021, he joined Loftwork, where he combines technology with a creative perspective to design products that contribute to user well-being. He also works on individual projects focused on the relationship between people and technology by incorporating the concept of Calm Technology. His hobbies include collecting gadgets and drinking tea.
In this project, we explored the new possibilities of smart textiles, which fuse textiles with digital technology. Smart textiles are generally applied to clothing and other items to provide or enhance functionality. However, aimed not only at improving functionality but also at making use of the unique features of Fujiyoshida’s textiles and enhancing their value. To this end, the project began with an exploration of the traditional weaving techniques of the city.
One of the distinctive features of Fujiyoshida’s textile industry is the “Jacquard weaving” technique. Using a specialized machine called a Jacquard loom, this technique weaves thousands to tens of thousands of fine threads at a high density, allowing for the creation of complex and three-dimensional patterns. On this occasion, we partnered with Hikari Textile Co. Ltd. to undertake the challenge of creating smart fabric by weaving “conductive threads” into the Jacquard weave.
Established in 1958, Hikari Textile primarily manufactures three-dimensional patterned textiles used in hanging scrolls, Japanese-style goods, and other products.
Conductive threads are threads that conduct electricity. We came up with the idea of creating and installation that reacted to touch thanks to the properties of static electricity, but soon encountered the fact that textiles are usually designed to minimize the generation of static electricity. Using conductive threads for textile production was a first-time challenge for Hikari Textile, so we engaged in a trial and error-process to determine how to weave the threads, which threads are suitable for the Jacquard loom, and which patterns are most appropriate.
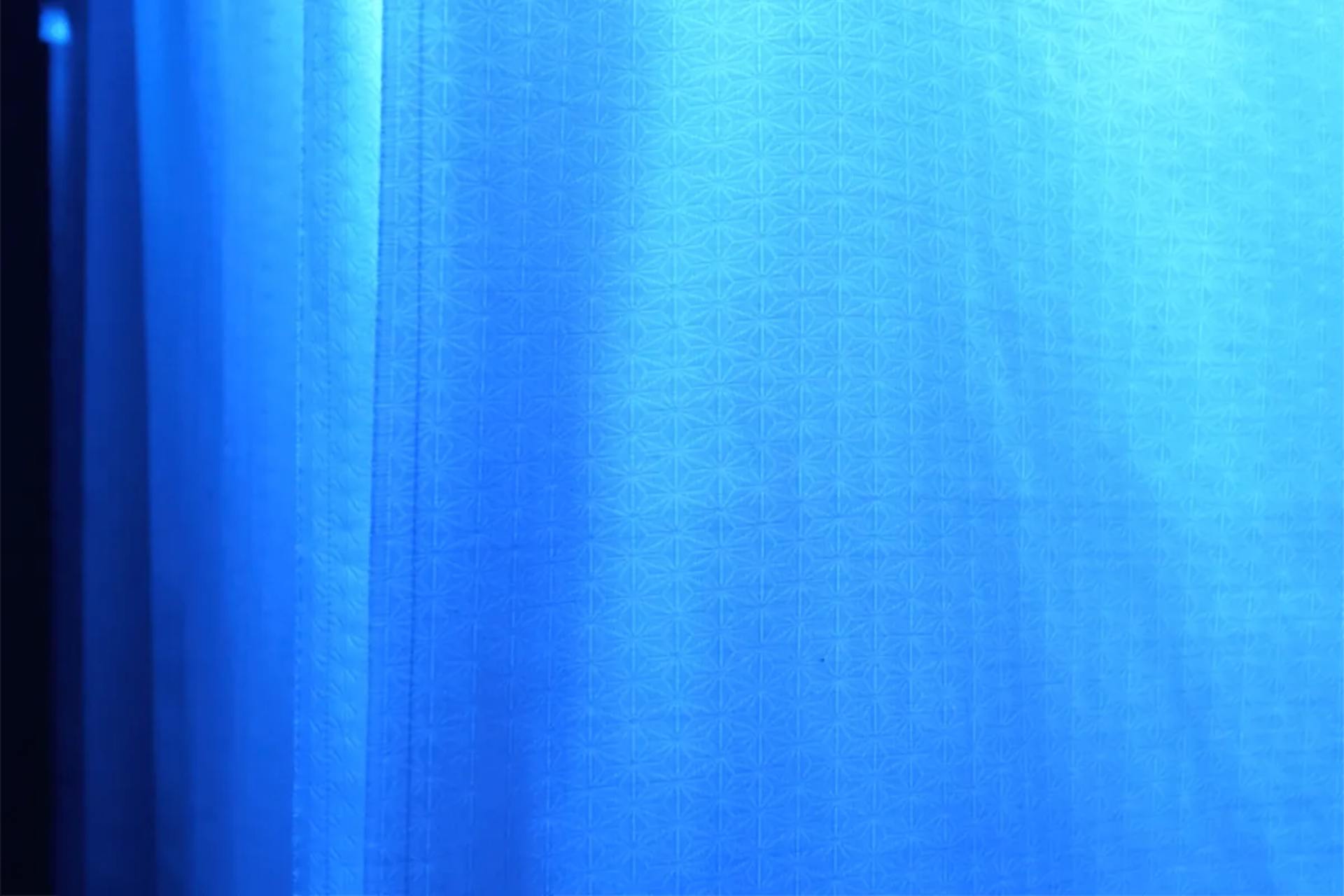
The textile pattern used in this piece is called asanoha (“hemp leaf”). It has a long history as a traditional Japanese weaving pattern.
In parallel to the discussions with Hikari Textile, we conducted several technical verifications on conductive threads.
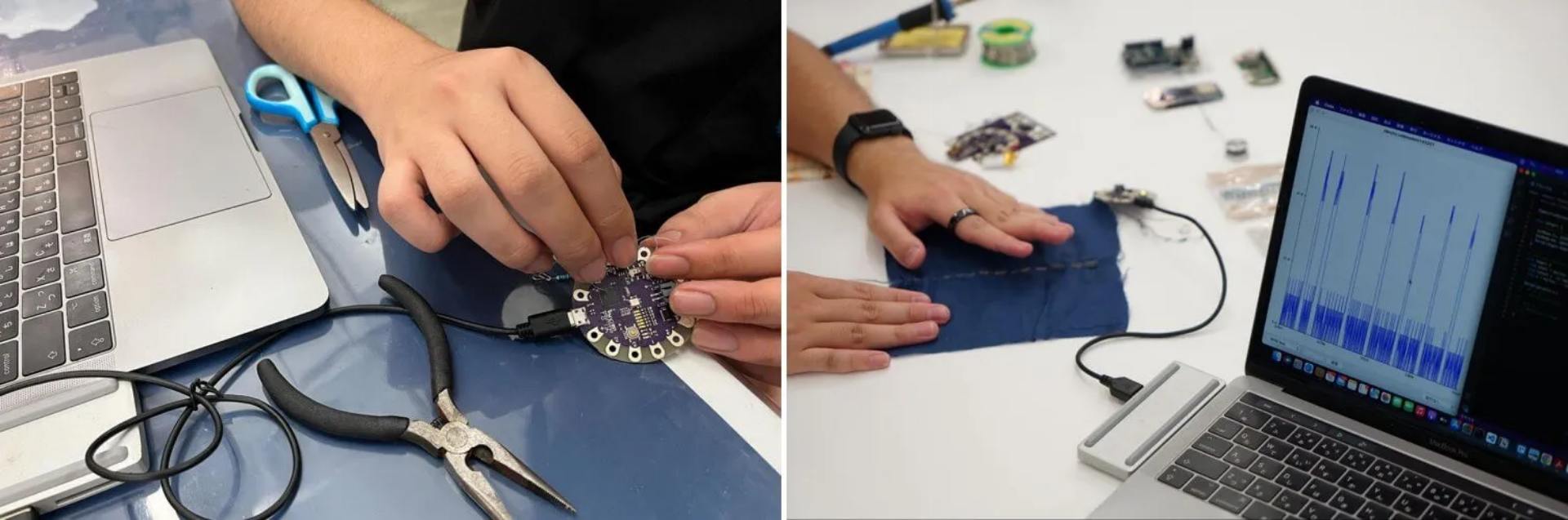
The team purchased conductive threads and a microcontroller to verify the sensitivity and the range of values that can be obtained when touching it.
We started by purchasing a microcontroller and conductive thread to verify the sensitivity and range of values that can be obtained when touching it. Afterwards, we asked Hikari Textile to weave test pieces using the same conductive thread we planned to use for this project. The yarn originally used in Jacquard machines is different from the conductive thread, so we needed to test the material at the manufacturing facilities to ensure the feasibility of the prototype.
After gathering basic verification results, we collaborated with creators to propose several ideas for the art installation and prototyped each of them in turn. After repeating this cycle for about a month, the team accumulated a growing body of knowledge and came gradually closer to a viable output.
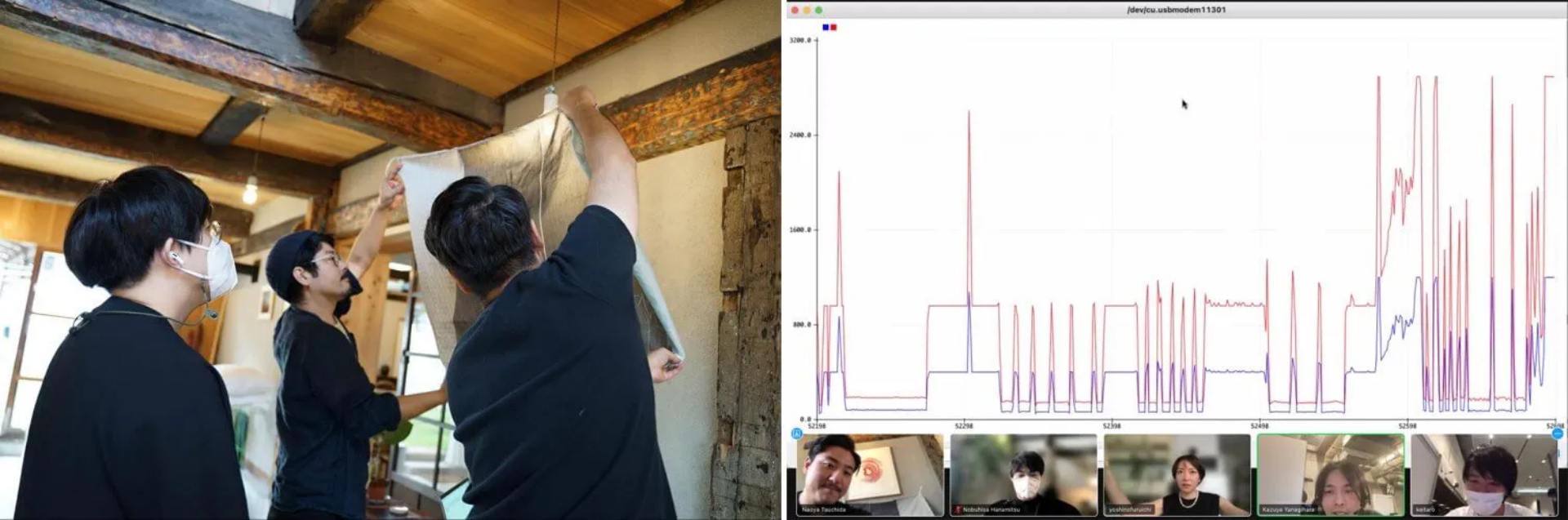
Various tests were undertaken, such as shining light on textile samples to check their transparency, or measuring the sensitivity of conductive fabrics.
Through technical validation, we were able to implement switch functions into the fabric. We designed it to respond not only to ON/OFF, but also to various types of touch, taking advantage of the unique tactile characteristics of the material.
As the next step, we brainstormed ideas with creators on how to utilize smart textiles in spatial environments. As we aimed to create a prototype that could be applied to future products, we needed to examine and validate the exhibition space while replicating the display environment. However, the exhibition venue, FabCafe Fuji, was under construction at the time, so we couldn’t enter the space until just before the installation.
To overcome this challenge, we applied digital technologies to simulate the environment and adjust accordingly. First, we used the 3D printer to reproduce the actual size of the space, and we confirmed the pattern of the textile and the direction of the installation. Then, we examined the color of the light and the pattern of the fabric, as well as the way the light changed when touched. We made detailed adjustments to the pattern of the textile, the color and amount of light, based on these tests. Even slight differences can greatly affect the quality of the experience, so we paid close attention to every detail.
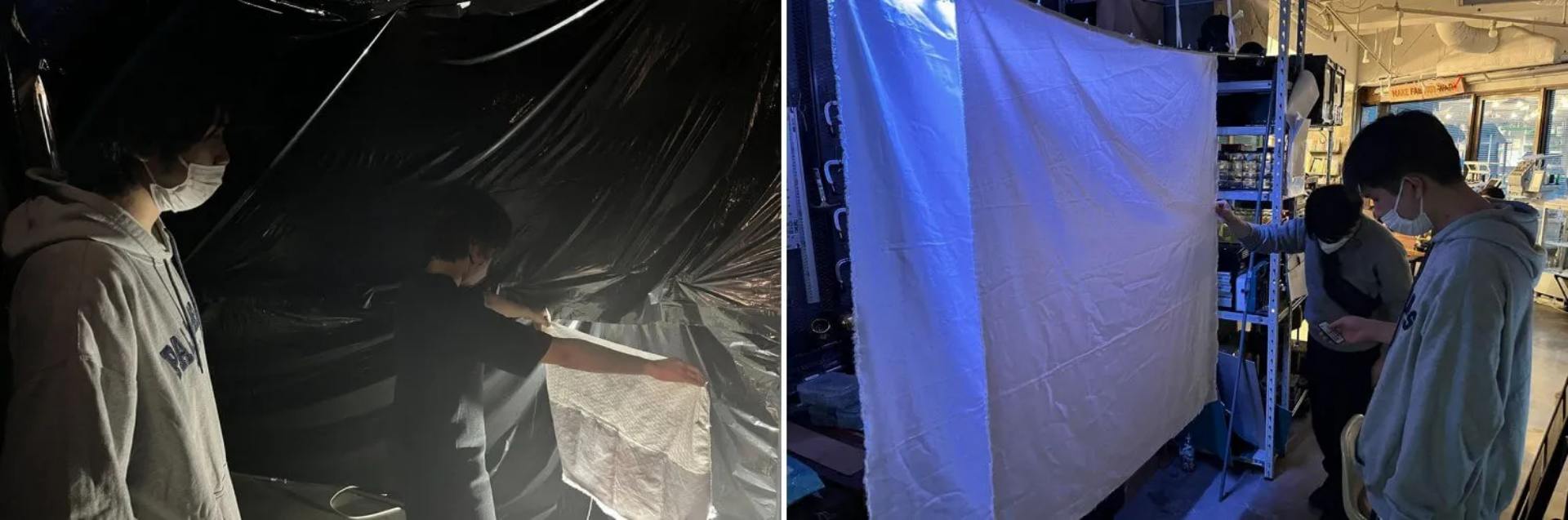
The team recreated an environment with the same level of darkness as the actual exhibition using a 3D printer, and adjusted the lighting and patterns by testing on the actual textiles, while also aligning the finer exhibition conditions such as ceiling height and floor materials.
In addition, the placement of textiles was verified in a virtual recreation of the exhibition area size. While alternating goggles, the team experienced the space in VR to confirm the lighting and spatial compression, and debated on the spatial arrangement, light conditions and more.
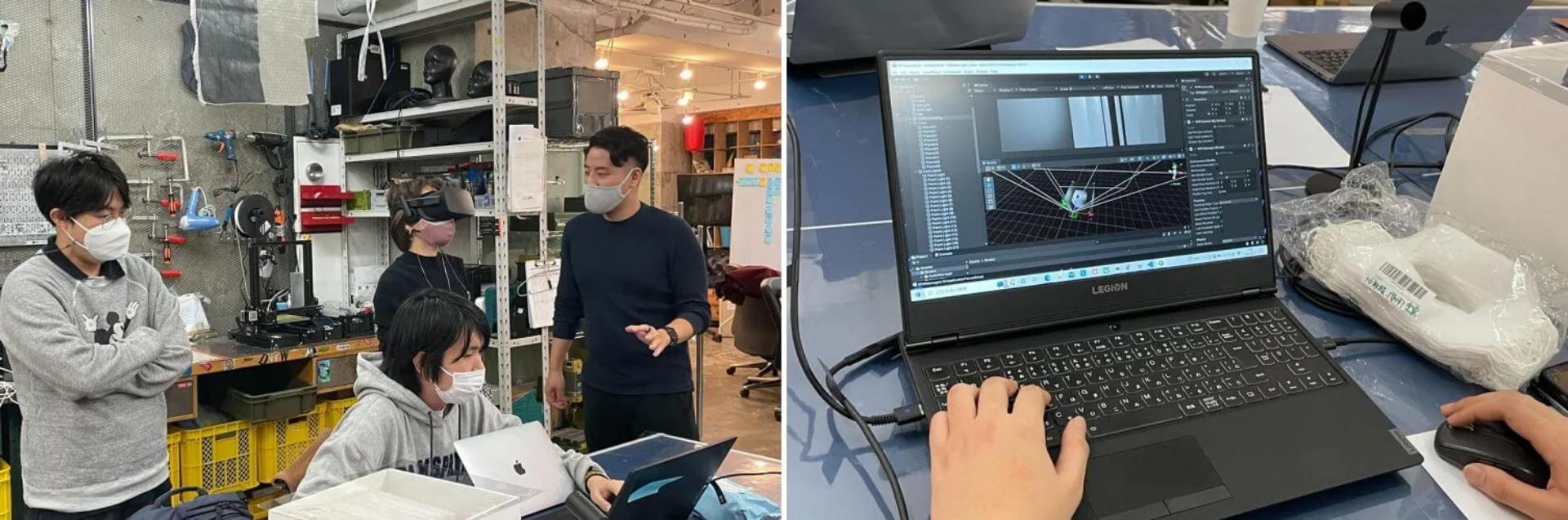
Based on the venue’s blueprint, they constructed a virtual space of the same size with Unity, and placed the textiles and recreated the exhibition experience in VR.
The success of this project is explained by the effective combination of the latest technology and Fujiyoshida’s traditional weaving techniques. By blending the perspectives and ideas of creators from various backgrounds, the Tech Working Group succeeded in creating a smart textile that promises exciting applications in architecture and space design.
The installation received enthusiastic feedback from the textile manufacturers who visited the Fuji Textile Week, many expressing interest in trying the fabric out for a range of products. Moving forward, the team now aims to design further refined products with specific applications.
When starting a project with the theme of “a spatial installation using smart textiles”, we had no samples and had to start from scratch to verify what kind of fabric we could use and what we could do with it. We struggled to understand how the fabric would work as a sensor, but through discussions with our team members, who could quickly turn vague images into tangible forms, we gradually formed a clear idea and were able to materialize it.
The light cube that swayed quietly in response to the environment looked like a living creature that inhabited that particular space. I was excited about its potential for further growth.
It was a great honor to be involved in such a stimulating project. Thank you very much.
Yoshino Furuichi, Yoshino Furuichi Architects & Engineers, Inc.
This time, we developed a fabric that conducts electricity. Unlike ordinary threads, we considered how to weave the fabric to maximize the properties of the conductive thread while making it look like ordinary fabric at the same time. We are very much looking forward to the future possibilities of the actual woven cloth. It is refreshing to seek out new findings and unexpectedness when developing unseen products, and I hope to continue to actively participate in this project in the future.
Takuya Kagami, Hikari Textile
Project Outline
- Project Manager: Naoya Tsuchida (Tech Working Group,Technical Director ,FabCafe and Loftwork)
- Support: Daiki Kanaoka (COO and CTO, FabCafe Tokyo), Kazuya Yanagihara (Creative Director, MTRL)
- Curator: Tsuyoshi Yagi (FabCafe Fuji)
- Installation design: Yoshino Furuichi (Yoshino Furuichi Architects)
- Installation implementation: Nobuhisa Hanamitsu (Enhance experience Inc. / Project Assistant Professor of Media Design, Keio University)
- Hardware design/implementation: Keitaro Tsuchiya
- Textile production: Hikari Textile
-
FabCafe Global Editorial Team
This articles is edited by FabCafe Global.
Please feel free to share your thoughts and opinions on this article with us.
→ Contact usThis articles is edited by FabCafe Global.
Please feel free to share your thoughts and opinions on this article with us.
→ Contact us