Project Case
June 12, 2019
FabCafe Global Editorial Team
The School of Architecture and Planning at The State University of New York at Buffalo conducts an annual study abroad program, which enables students to embed themselves in an unfamiliar culture while earning University credits.
FabCafe Tokyo and FabCafe Hida provided the hub for this study abroad program as well as put together and operated the key features of a 5-day “Hida Residency Program”. (→See the Project page)
Students visited the workplaces of woodworking craftsmen and furniture builders, learned woodworking skills (in particular, coupling and wood conjoining techniques) from these professionals. Through a production process operated by FabCafe Hida, using 3D modeling technology, students created new works of Japanese traditional kumiki (interlocking wooden building blocks).
The overseeing faculty member, Assistant Professor Nicholas Bruscia, and Project Manager & Director Daiki Kanaoka of FabCafe, who, as they looked back on the experience of this program, both agreed that, “Over the course of this 9-week Study Abroad Program, it was the Hida Residency Program which turned out to be the most in-depth and educational experience for these students.”
Interview & text by Mariko Suzuki
“Study Abroad Program” – where students immerse themselves for 9 weeks in an unfamiliar culture
– Professor Bruscia, how would you describe the study abroad program” which you are overseeing?
Bruscia: In this program, for one term (9 weeks), students will earn university credits while studying overseas. Since I became in charge of this program in 2010, we have conducted it every few years, and each time we have made Japan the study abroad country.
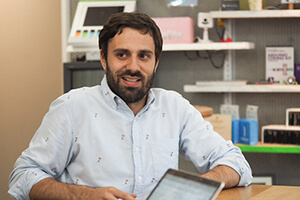
Clinical Assistant Professor Nick Bruscia of School of Architecture and Planning, University at Buffalo, the State University of New York
– Professor Bruscia, why did you select Japan? And when did you learn about FabCafe?
Bruscia: When I was a student, I studied in Japan. And when I was placed in charge of this program at my university, it made me very happy. When FabCafe opened in 2012, I would use FabCafe Tokyo to prepare for classes and do my work, and as I became friendly with the staff, I discovered that there were many among the FabCafe Tokyo team members who specialized in architecture, so in 2014, we did a workshop together with KOIL.
– What led FabCafe to operate this year’s study abroad program?
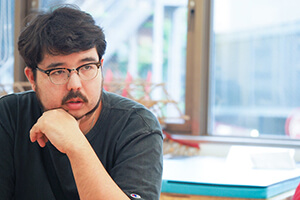
Kanaoka: When Professor Bruscia and his colleagues visited Japan last year, we had them drop by FabCafe Hida. We took them to see the major hubs of Hida’s woodworking industry, and on strolls through the forests. Professor Bruscia let us know that he would like to do the Study Abroad Program again this year, and that he would like to visit Hida again. He requested that this time we arrange not just for visits and observations in Hida, but for opportunities for students to learn through the actual production process.
Furthermore, he also requested that the central hub in Japan during those 9 weeks be at FabCafe MTRL in Shibuya. FabCafe MTRL is an open co-working space where people can drop in freely, and holds events nightly. By making FabCafe MTRL the central hub, students can connect to a diverse group of Japanese people.
– What kinds of goals did you establish for this year’s Hida Residency Program?
Kanaoka: In Hida, by combining traditional Japanese woodworking techniques of “kumiki” with new design processes featuring 3D modeling, our goals were to help students explore new possibilities in traditional arts and discover new ways of using cutting-edge technologies.
To get down to specifics, we had students reside at FabCafe Hida for 5 days. They visited the workplaces of woodworking craftsmen and furniture builders, and learned woodworking skills, especially coupling and joint techniques. From there, we had them spend 2 days in production, using 3D modeling technology to take on the challenge of building a kumiki project. They would receive feedback from actual woodworking professionals on their kumiki, and had their processing skills reviewed and scrutinized.
Bruscia: For that purpose, we assigned the students in the Hida Residency Program this project to create a “new kind of kumiki design” utilizing the latest 3D modeling technologies.
– What was it like for the students to experience the process of actually making kumiki in the studio at FabCafe Hida?
Bruscia: The students are used to making prototypes in the U.S. but they had never tried building something so complicated as this. The production staff at FabCafe Hida helped them with using the equipment and through this, the students learned many things during the experience.
– How did the students do in response to their assignment to “design a new type of kumiki”?
Bruscia: The students split up into 3 teams to build their kumiki, and produced a total of 8 new kumiki designs. I had decided that, for this design project, there was only one way to find out if their ideas were actually produce-able, architecturally viable, and aesthetically interesting. And that was to actually go through the production process at Hida, through an actual, hands-on process. This, I believe, was where the students learned the most.
Kanaoka: The students created some unusual and unexpected kumiki designs that surprised even the Hida carpenters.
Team building and local cooperation were the keys to the success of this program
– I heard that you and Assistant Professor Bruscia developed a jig that utilized 3D modeling technology and sensors.
Kanaoka: I had Junichiro Horikawa (an architectural programmer and designer) join us as a technical support member to build a jig that utilized sensors. This is a tool that would use sensors to process kumiki designs created using 3D modeling data, and could even handle complicated three-dimensional angles as well. Instead of using robot arms or other such complicated machine tools that required high-level operational skills, our goal was to create an easy-to-use, flexible and affordably designed jig that could be used as an attachment to a normal band saw.
Bruscia: I believe that this tool has enormous potential. 100% digital and analog. It’s a way of building that straddles the gap between the two. Daiki Kanaoka assembled the perfect team for this project. I think that this project would not be possible if even a single member were missing. There were several difficult hurdles we had to clear, but thanks to Junichiro Horikawa’s programming skills and knowledge about sensors, we made it through. The three of us got together at FabCafe practically every weekend to hold discussions.
Kanaoka: And the three of us often took trips to Akihabara to look for parts (laughs).
– In Hida, you programmed several opportunities to closely observe a variety of craftsmen at work. I heard that a demonstration performed by Mr. Tanaka (a carpenter) had a particularly influential effect on the students.
Bruscia: The visits to see the carpenters and the demonstrations were an unforgettable experience for the students. After all, seeing the carpenters work with their own eyes was incredible. With regard to kumiki, they could listen to professionals talk, read books about it, and understand it conceptually. And while they could observe how it was used in buildings, to be able to actually see it being built before their very eyes was a deeply impressive experience for all of the students.
When I asked them, “What part of this experience during the residency in Hida left the biggest impression?”, one student replied, “They (the carpenters and craftsmen) have a deep respect for wood.” He said that these craftsmen respected, understood, and listened to the voices of the wood. It touched me deeply to hear my students speaking in this way. I believe that, given this opportunity to see how these professionals worked up close, the students felt that they needed to seriously engage with this project.
How to design an “experience that feels like living”
– What role did the Hida Residency Program play within the study abroad program itself?
Bruscia: The residency in Hida was for a short period of only 5 days, but counted for over half of the units available on this study abroad program.
Looking back on the entire program, I feel that the experience that the students gained during the Hida Residency Program was the most valuable. In the end, their residency in Hida was, rather than just a visit, more like the experience of actually living there. I believe that architecture is not just about the design of a building, but requires an understanding of the context that exists behind it. It is very important to know the city, and its culture. I feel that we accomplished more than we ever expected with this Hida residency.
Kanaoka: I hope we can continue to build this hands-on program together. I look forward to it.
-
FabCafe Global Editorial Team
This articles is edited by FabCafe Global.
Please feel free to share your thoughts and opinions on this article with us.
→ Contact usThis articles is edited by FabCafe Global.
Please feel free to share your thoughts and opinions on this article with us.
→ Contact us